​Kristen Heaton
Spring 2017- Design Two
Throughout this semester, I worked on a team of six people to design and build a human powered vehicle for our end user, who has spastic diplegia cerebral palsy. I learned more about bicycle components and subsystems while meeting frequently to test ideas with our end user and gain expertise from a local Harrisonburg bicycle expert. I also took on an organizational role by keeping track of team meeting accomplishments, helping to set meeting agendas, and ordering needed components to aid in the final assembly of the bicycle.
The following images display the three proof of concepts that a sub-team and I created to test the functionality of a swivel seat idea we wanted to integrate into our vehicle so that our rider could mount and dismount with ease. Through these tests, we found that lower top and bottom tubes on the frame would serve our purpose.

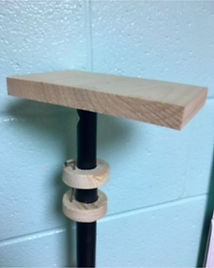
To test the function of a swivel seat, my team brainstormed and created two prototypes so that when each mechanism was activated, would allow the seat to rotate in the direction the seated user desired. The left image was activated by a spring-loaded lever with a recessed pin that when pressed, the moved pin allowed the seat to rotate. The right image was activated by removing a pin that would allow the top tube with attached seat to rotate freely until the locking mechanism was reengaged.

For the second proof of concept, a fellow team member built a prototype to test the rotating seat function on a larger scale. The base of a stool [1] was chosen to allow the seat to rotate while reducing tipping. A seat with a backrest [2] was attached to the top of the stool that would provide comfort as well as back support during the testing. A thin piece of wood was attached to the stool to simulate a bike frame top tube [3].


For our third and final proof of concept, my team changed how the top tube was simulated based on our experience we had with testing our second proof of concept with our end user. With the lowered top tube, our end user found it easier to get on the seat. With this finding, our team determined that a lowered top tube on the bike frame removed the need for the swiveling seat.


Another part of this human powered vehicle project was to 3D model in SolidWorks all of the design's components. I was assigned to do the handlebars and a seat back rest, which was ultimately not built. The left image are the handlebars, the right is the back rest which was to slide over the seat tube.
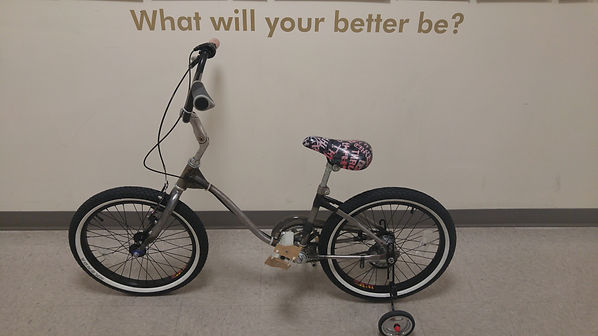
Through constant effort of my team throughout the last few months of the semester, we were able to build a bike that our end user got to ride in early May along with eleven other bikes designed and built by other teams. This bike and the other designs allowed me to build a final human powered vehicle for my end user over the summer.
To see how these twelve human powered vehicles culminated to a final design, click on this button here.